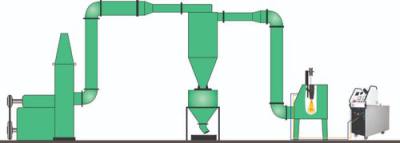
Online Zinc Spray For Tube Mill Plant coating system on G. I. Tubes and pipes produced from Tube Mills generally lack corrosion resistance property at weld portion, throughout the entire Seam Spraying of Pre-coated E.R.W Tube length (due to removal of the galvanized layer while welding the seam) resulting in poor corrosion resistance and subsequent rusting.
The metal coat has analyzed the problem and developed chemically non-hazardous thermal spray gun system for continuous online zinc spray coating on G. I. Tubes and Pipes on the seam. Such systems have been confirmed and supplied to various leading tube mills where these systems have been performing satisfactorily.
The metal coat has investigated the issue and created chemically non-hazardous thermal spray coating systems for continuous online zinc spray coating on G. I. Tubes and Pipes at the seam. Such systems have been verified and supplied to a number of renowned tube mills, where they have performed admirably.
The Zinc spray is 20 to 30 Microns. However, 10 to 100 microns can be deposited (depending upon tube/pipe traverse rate) on Tubes and Pipes ranging from 15mm N.B. to 125mm N.B. Size without interrupting Tube Mill speed. The ordinary output can be 10 pipes per minute with an estimated 25 microns coating thickness. The System package consists of a dry spray room (Spray Chamber), Twin Cyclone, Exhaust Fan with motor along with ducting.
Zinc Spray for Tube Mill Plant for The Spray Booth
The Zinc Spray for Tube Mill Plant is installed just after the welding Work Station. The Arc Spray Gun is positioned inside the Spray Booth. The distance of the spray gun from the tube/pipe is adjusted depending upon the size of the tube/pipe and the spray pattern required to minimize spray wire losses. The Hot Weld seam is sprayed with zinc wire resulting in a dense coating with a strong metallurgical bond over the weld seam.
The fumes and fine Zinc dust generated in the spray booth are sucked into the cyclone dust collector due to suction created by the exhaust fan. Due to cyclonic action, the zinc particles are trapped at the bottom of the cyclone dust collector, and clean air is discharged from the outlet of the blower into the atmosphere keeping The thermal spray booth consists & of Arc Spray Gun with a two-wire feeding arrangement DC/AC Power source built-in with control console with wire spool stand having spool capacity 15Kgs each.
The Wire feeding device is by pull process powered by an electric motor. The wire feeding speed is adjustable through the motor. The zinc spraying coating system is a cool process producing fine and dense quality coating having high bonding strength and the smallest porosity
Spray Booth for Metalizing Zinc Spray for Tube Mill Plant
Metalizing Spray Booth design will reduce cylinder manufacturers' difficulties, which were previously caused by greater production needs and inconsistent manual coating work. For more than 20 years, Airo Shot Blast India has been a leader in the development of metalizing spray booth equipment. The company's key strength is to design and manufacture thermal spray painting equipment as well as automation.
LPG Cylinder Blasting Booth is composed of:
- Blasting Chamber
- Lower cabin with the helical mover
- LPG Cylinder Rotation and Moving System
- Elevator
- Sift & Separator
- Dry Filter Unit (dust collector)
Zinc Spray System for Tube Mill in India
We are the best Online Zinc Spray for Tube Mill Plant coating system Manufacturer, supplier, and Exporter in India for Tube Mill Industry. Aero Shot Blast is the Best Shot Blasting Machine Manufacturers in India. We provide Sand blasting Machine, shot blasting machine, grit blasting machine, thermal spray gun, shot blasting cabinet, pressure blasting cabinet, arc spray gun, metalizing gun, flame spray gun, at a low price for sale, etc Jodhpur, Rajasthan, India with the best quality.
Quick Inquiry